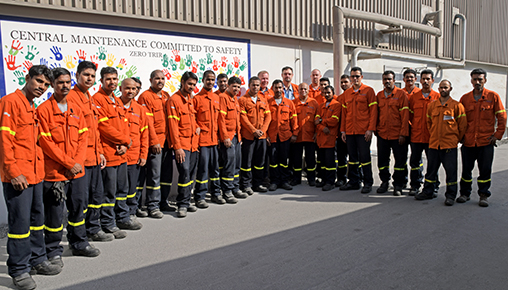
Efficient HVAC systems are critical to Qatalum's success as without proper cooling the equipment as well as the employees cannot function at their optimum. Some of the equipment which rely heavily on HVAC include GIS substations, Excitation panels, HV MCC & ISIT Server rooms, PTM's, FTA's, MTV's ,SAW, Transfer and Silo tower, Cruissable & Hydrogen chillers, Panel AC's of RCCP, Swarf & Ramp, Operational vehicles and Cool booths during peak summer season.
Despite its significance, the HVAC section was faced with growing challenges in exercising full control of HVAC equipment given the extensive workload of more than 1500 functional locations, enormous work orders and limited manpower. The approach had been reactive in the past due to the heavy breakdown in all HVAC systems whilst the control over the maintenance was not at par. With the team effort and motivation from department manager under the guidance of Chief Technical Officer, the situation improved.
The Chief Technical officer,Geir Nilsen applauded the efforts in these words "The HVAC team is for me a school example on what can be achieved, if you have a dedicated team that work systematically according to QPS principles. Outstanding results. Thank you HVAC team for showing us how continuous improvement work is done."
The Central Maintenance Manager, Daniel Els commented "The HVAC team has made great improvement to all the HVAC systems and processes at Qatalum over the years, with the use of the QPS tools, and this is much appreciated. With their focus on continuous improvement this is sure to continue into the future"
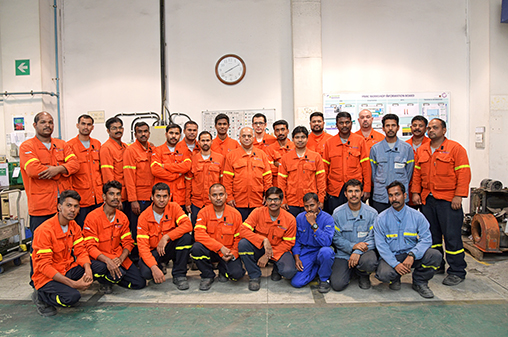
The efforts to tackle these challenges commenced in 2014. QPS tools were employed to identify the exact problem and to prevent engineering high cost solutions in several areas. QPS team extended support in optimization of PM plans. Various trainings and workshops were conducted to achieve improvements as part of QPS way of finding the root causes to trouble shoot.
As part of the Cost improvement project, the numbers of contractor were brought down from 56 in 2013 to 26 in 2018 by performing Network Analysis to optimize the HVAC contractor team. This included demobilization of six contractor supervisors, two planners and one HVAC engineer along with technicians.
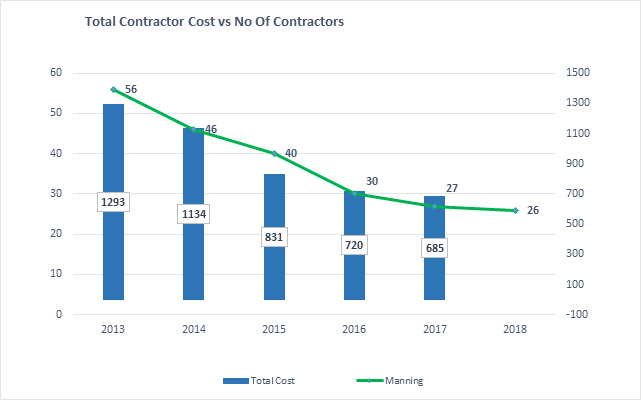
The introduction of the new HVAC workflow was one of the major initiatives, which redefined the roles and responsibilities of Qatalum team clearly. The earlier dependence on the Contractor team was no more as the HVAC responsibility was transferred to Qatalum team resulting in better control of HVAC systems. To deal with the drastic reduction in contractor manpower, new PM plans were introduced in coordination with Area owners who were also transferred the responsibility of first line maintenance and routine inspections.
RCAs were conducted to bring about improvements with the help of Area owners. In the past, recurrent leakages of HVAC Condenser coil leakage of 305 Sub stations incurred high maintenance cost, and impacted availability of critical equipment. This was resolved by replacing the coils with locally fabricated ones. A total of 80 coils were replaced for all high voltage MCC rooms. In the power plant, the Air drier was modified instead of purchasing new units to avoid additional costs.
Modification on Carbon Heating ramp panel units and FTA local cooling coils and cabin A/C were carried out to improve efficiency & reliability also aimed to reduce maintenance cost. Rectifiers HVAC panel A/C's were modified by providing additional insulation on panel A/C's and provided weather protective shed & frame to avoid frequent tripping due to high ambient temperature and for easy maintenance access.
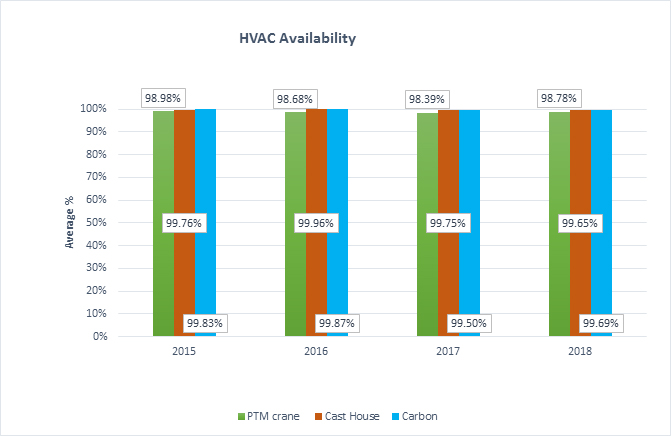
Frequent breakdowns in PTM HVAC units due to the OEM coil failure had been tackled by introducing improved, locally fabricated, low cost, better life coils on TT2, TT1 HVAC units. Local low cost Condenser fan motors upgraded type were introduced and replaced 128 motors for FTP Electrical rooms there by improving efficiency & reliability and reducing maintenance cost. High cost refrigerant replaced with alternate low cost suppliers for PTM HVAC units. Honeywell controllers replaced with Allen Bradley in coordination with Automation in Reduction and Carbon for ensuring 100% software back up facility with in Qatalum.
Proposed safe working platform to access PTM cabin and TT2 AC units which is ongoing at the moment. Due to the phase out refrigerant (Retrofit of Refrigerant), OEM recommended to replace the Reduction service cranes HVAC units, however the team has successfully modified the service crane instead of replacing and the task is in progress for the remaining cranes. Replaced 12 no's pot line operator room A/C's which is effective and easy to access for maintenance.
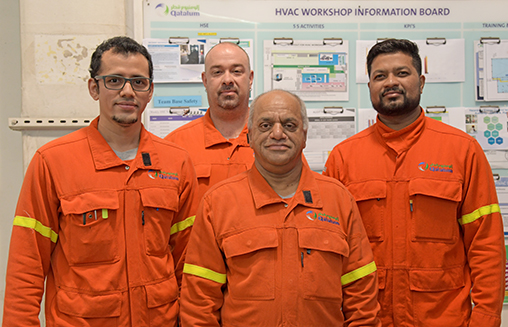
Relocation of split units for easy maintenance access in cast house and plant was actioned to avoid frequent scaffolding requirement. Installed additional A/C units in Cast house Dross press MCC room for which the unit was arranged from Project surplus item. In mould shop condenser coils of HVAC units were replaced with locally fabricated ones which improved reliability of the systems.
In general, the HVAC team introduced locally fabricated filters plant wide to avoid high cost OEM filters. Another initiative undertaken was to arrange new MM's for OPM parts to avoid high cost OEM parts. Replacement of condenser coils plant wide are ongoing based on the deteriorated condition. OEM inspections by AMC in Common building chillers were stopped and responsibility assigned to in house team. Lab XRF-XRD chillers were repaired which is an achievement, as OEM refused to assist for the repair and their advice was to replace the chillers by mentioning that it is not suitable for high ambient temperature.
These efforts are notable as they resulted in conspicuous cost savings. Cost saving in HVAC spares through local cost-effective source, HVAC modification & improvement are calculated at 137,500 USD till date. Between 2014 and 2017, the cost savings on contracted man power is 604,700 USD. In-house maintenance takeover from annual maintenance contract of screw chillers with OEM helped save 18,690 USD in the year 2015-2016. It is worth mentioning that the curtailment on Maintenance cost, spares and manpower were achieved by not compromising Safety and ensuring Reliability of critical equipment at Qatalum.